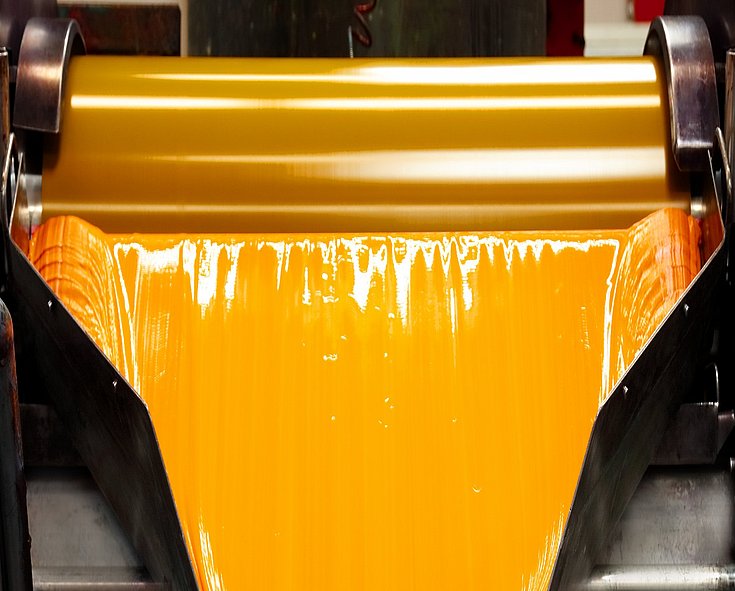
Colors are passion, emotions and personality. At Siegwerk, inks and coatings are our specialty and we use color to bring the packaging and products of our customers to life.
For the most important printing defaults causes and solutions listed in this guide in order to help you to identify your problem. For further details, please contact your Siegwerk representative. The paper & board printing guide published by Siegwerk offers you the possibility of quickly identifying and correcting problems so that you can increase your printing productivity.
Unprinted areas appear at the bottom of the flutes and form bands larger in the centre of the board sheet
Causes:
Solutions:
Comment: Prepare a plate with mounting foam. Be careful: an increase of the pressure between the press cylinder and the board will emphasize the phenomenon. The only solution is to slow down the machine.
The color strength varies in comparison to previous prints or samples.
Causes if the color strength is too weak:
Solutions if the color strength is too weak:
Causes if the color strength is too high:
Solutions if the color strength is too weak:
The bottom of the flutes are not sufficiently inked.
Causes:
Solutions:
Non printed areas appear randomly. Non printed areas are due to the crushing of the board sheet and will produce similar zones with an excess of ink on the following sheet.
Causes:
Solutions:
Spots like small or big shooting stars appear.
Causes:
Solutions:
The shape of the screen dot in the print deviates considerably from the original shape.
Causes:
Solutions:
The screen dot is surrounded by a line or a ring.
Causes:
Solutions:
Spots are present outside the printed area.
Causes:
Solutions:
Colored constituents of the printing ink become visible in parts of the motif which have not been printed.
Causes:
Solutions:
Dots are larger than expected – usual phenomenon observed in flexography which reduces the details and the contrast.
Causes:
Solutions:
In areas with a high ink coverage, the colour overprint is not correct.
Causes:
Solutions:
Comment: Choosing colours sequence: K, C, M, Y might reduce the effect.
The colour density is higher on the top of the flutes – this is due to the resistance of the flute which caused dot gain.
Causes:
Solutions:
A lack of ink appears at the limits of the back edge, in the running direction.
Causes:
Solutions:
Bridges are created between dots
Causes:
Solutions:
Changes of colour along the machine width.
Causes:
Solutions:
Overflow of ink on relief contours of the plate.
Causes:
Solutions:
Dust particles on the substrate cause spots and defects. This is the case with solid printing, where white spots are surrounded by a lighter ‚halo‘.
Causes:
Solutions:
Comment: Use antistatic unit or antistatic brushes.
Foam visible in ink pail or pump, missing print areas.
Causes:
Solutions:
Comment: Excessive and incorrect addition of defoamer leads to “Pinholing”, in this case wash and rinse the printing unit and fill with fresh ink.
The ghosting effect is a weak printed image that is visible in one part of the motif where it should not be. Usually this effect occurs in the case of a solid print with negative text or with windows.
Causes:
Solutions:
Printing error owing to parallel lines (clear or dark) in the direction of printing.
Causes:
Solutions:
Uneven printing on text edges or in lines.
Causes:
Solutions:
In the overprinting of the process colors (CYMK) the individual grid structures can interact and create a pattern. The type of interaction can create an undesirable interference pattern, the so-called moiré effect.
Causes:
Solutions:
Uneven ink layer in solid printing – this printing defect frequently appears on coated papers.
Causes:
Solutions:
When printing & die-cutting, the ink is torn off by the die-cutter press.
Causes:
Solutions:
Clear or dark spots appear and shift in the print areas.
Causes:
Solutions:
Comment: This effect can appear with half-tone.
The solid printing is made of dark and irregular lines – this effect is observed only with a two roll system.
Causes:
Solutions: