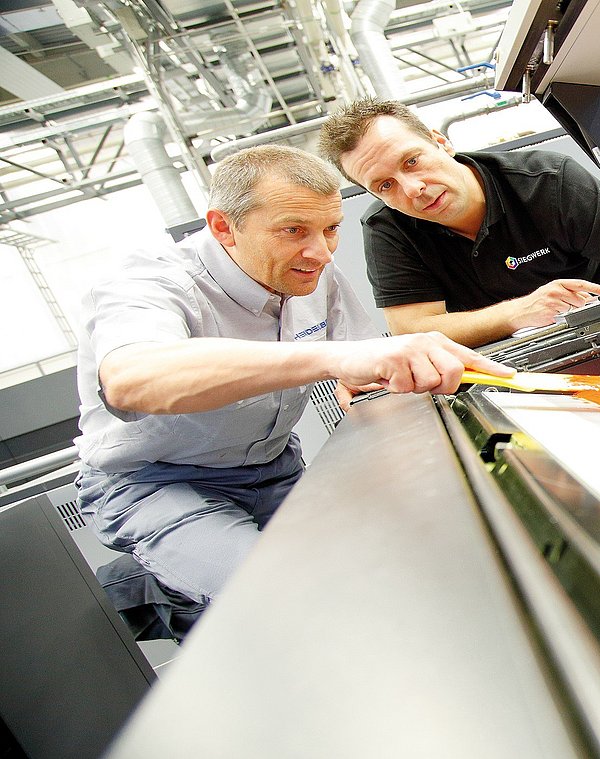
Papier & Karton Ratgeber
In unserem FAQ erhalten Sie sofortige Lösungen rund um das Thema Paper & Board
Fragen und Antworten zum Thema Farbstärke
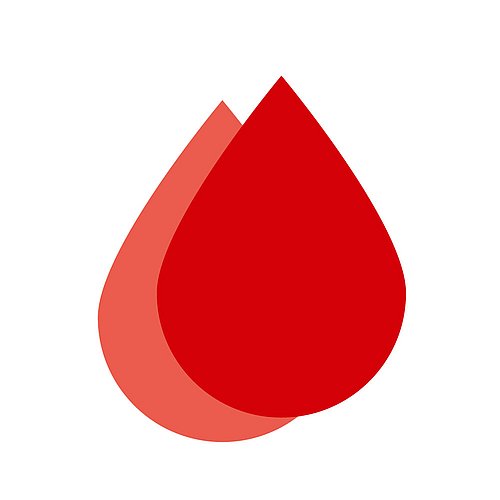
Gründe:
- Der Farbton der verwendeten Druckfarbe ist zu stark
- Die Viskosität der Druckfarbe ist zu hoch
- Das übertragene Farbvolumen ist zu hoch
Lösungen:
- Durch Zugabe von Verschnitt die Farbstärke reduzieren
- Die Auslaufzeit durch Zugabe von Wasser reduzieren
- Eine Rasterwalze mit niedrigerem Schöpfvolumen einsetzen
Gründe:
- Die Farbe trocknet auf der Rasterwalze
- Der Farbton der verwendeten Druckfarbe ist zu schwach
- Die Auslaufzeit der Druckfarbe ist zu niedrig
- Die Rasterwalze ist verschlissen
- Das übertragene Farbvolumen ist zu niedrig
- Die Druckfarbe ist für diese Anwendung nicht geeignet
Lösungen:
- Die Rasterwalze reinigen
- Den Farblieferanten kontaktieren, falls möglich Konzentrat hinzufügen
- Die Viskosität durch Zugabe frischer Druckfarbe erhöhen
- Die Rasterwalze ersetzen
- Eine Rasterwalze mit höherem Schöpfvolumen einsetzen
- Den Farblieferanten kontaktieren
Gründe:
- Die Wellpappe ist nicht für den Druckauftrag geeignet
- Die Wellpappe ist zu nass
- In der WPA wird zu viel Stärke und Hitze verwendet
- Die Druckplatte ist zu hart für diese Wellpappenart
- Die Kombination Papier/Druckplatte ist nicht korrekt
Lösungen:
- Andere Wellpappe verwenden
- Die vollständige Trocknung der Wellpappe abwarten
- Die WPA-Einstellungen optimieren
- Bei A-, B- und C-Wellen die Shore-Härte der Druckplatte überprüfen
- Eine Druckplatte aus anderem Material testen
- Eine Rasterwalze mit hohem Schöpfvolumen einsetzen
Fragen und Antworten zu Druckpunkten und Farbpunkten
Gründe:
- Der Wellpappenbogen wurde beschädigt oder die Produktionseinstellungen in der WPA sind nicht korrekt.
Lösungen:
- Den Wellpappenbogen während jedes Prozessschrittes vorsichtig behandeln.
- Möglichkeiten der Beschädigung vermeiden.
Gründe:
- Das übertragene Farbvolumen ist zu hoch
- Die Oberflächenspannung der Druckfarbe ist zu hoch
- Die Druckgeschwindigkeit ist zu hoch
- Die Absorption des Substrats ist ungenügend
- Die Abriebfestigkeit der Druckfarbe ist nicht gut
- In der WPA wird zu viel Hitze verwendet
Lösungen:
- Die Rasterwalze austauschen oder Viskosität verringern
- Ein Benetzungsmittel hinzufügen, um die Oberflächenspannung herabzusetzen
- Die Druckgeschwindigkeit verringern und die Trocknung der Druckfarbe optimieren
- Benetzungsmittel hinzufügen oder die Viskosität reduzieren
- Die Farbrezeptur überprüfen und ggf. umformulieren
- Ein Wachsadditiv unter Rühren hinzufügen
- Die WPA-Einstellungen optimieren
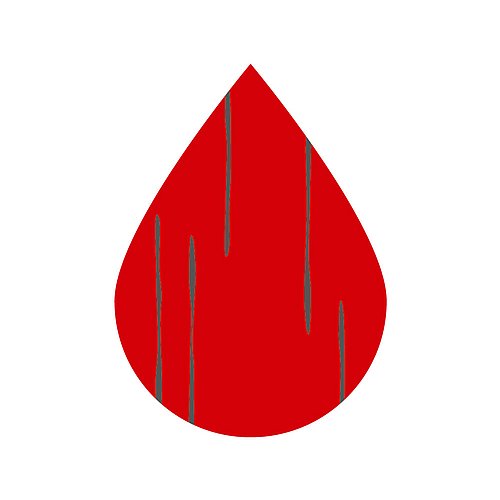
Gründe:
- Die Druckeinheit ist unzureichend gereinigt worden. Trockene Farbagglomerate werden zwischen Rasterwalze und Kammerrakel zermahlen und auf die Druckplatte übertragen.
- Zu hoher Farbauftrag: Feine Partikel trockener Druckfarbe bilden sich am Rand von Schriften/Motiven und werden in der nachfolgenden Druckeinheit verschleppt.
Lösungen:
- Die Druckeinheit reinigen und gegebenenfalls über die Installation einer Filterung nachdenken
- Verzögerer hinzufügen
- Verringerung des Farbvolumens durch Einsatz einer Rasterwalze mit niedrigerem Schöpfvolumen oder Verzögerer hinzufügen
- Das Verhältnis von Verschnitt zu Konzentrat überprüfen und falls notwendig Verschnitt hinzufügen
Gründe:
- Die Druckplatte ist zu weich
- Die Dicke der Druckplatte ist zu hoch
- Übermäßig starke Schwankungen in der Dicke der Druckplatte oder des Klebebandes
- Der Anpressdruck zwischen der Druckplatte und dem Substrat ist zu hoch
Lösungen:
- Eine Druckplatte mit höherer Shore-Härte verwenden
- Eine Druckplatte mit korrekten Einstellungen verwenden
- Die Druckplatte austauschen oder ein anderes Klebeband verwenden
- Den Anpressdruck reduzieren
Gründe:
- Die Höhe der Druckplatte und/oder des Klebebandes ist zu dick
- Die Druckplatte ist zu weich oder das verwendete Klebeband ist zu hart
- Der Anpressdruck zwischen der Druckplatte und dem Substrat ist zu hoch
Lösungen:
- Die Druckplatte austauschen oder ein anderes Klebeband verwenden
- Den Anpressdruck reduzieren
Gründe:
- Die Druckeinstellung zwischen Druckzylinder und Substrat ist zu hoch
Lösungen:
- Die Druckeinstellung reduzieren
Gründe:
- Auf die Rasterwalze wird zu viel Druckfarbe übertragen, sodass bei hohen Druckgeschwindigkeiten kleine Farbtropfen auf das Substrat geschleudert werden
Lösungen:
Alle möglichen Parameter für den Ursprung des Farbüberschusses prüfen:
- Die Viskosität ist zu hoch
- Die Druckeinstellung zwischen Druckzylinder und Substrat ist nicht korrekt
- Druckfarbe neu formulieren, Farbhersteller kontaktieren
Fragen und Antworten zur Farbdichte
Gründe:
- Dieser Effekt tritt bei steifen Bögen, wie Mikrowellen oder Bögen mit hoher Grammatur auf
- Die Klischee- oder Druckwalzenhärte ist die Ursache des Problems
- Druckplatte: Die Führungskante ist sehr groß
Lösungen:
- Druckplatte: Die Stützkante ist zu groß
- Die Shore-Härte überprüfen
- Den Maschinenhersteller kontaktieren
- Sofern möglich, Anpassung entsprechend des finalen Designs vornehmen
- Die Druckplatte mit Montageschaum erstellen
- Vorsicht: Eine Verbesserung des Druckergebnisses kann eine reduzierte Geschwindigkeit herbeiführen
Gründe:
- Farbauftrag im Überdruck ist zu hoch
- Unvollständige Trocknung der Druckfarbe
- Der Effekt tritt beim Wellpappendruck hauptsächlich im Wellental auf, speziell bei Wellpappenbögen mit niedriger Grammatur
Lösungen:
- Das Drucken von zwei Farben mit 100% vermeiden
- Die Farbmenge auf der Druckplatte reduzieren oder für große Wellen eine andere Druckplatte verwenden
- Die Farbqualität und die Effizienz der Trocknung überprüfen
- Die Welle ist zu groß, das Deckenpapier ist zu dünn oder von zu geringer Qualität
- Ein Benetzungsmittel hinzufügen
- Die Viskosität reduzieren
Durch die Einstellung der Farbreihenfolge K, C, M, Y kann dieser Effekt reduziert werden
Gründe:
- Der Bogenaufbau ist nicht geeignet
- Die Härte der Druckplatte ist nicht auf die Welle abgestimmt
- In der WPA wird zu viel Stärke und Hitze verwendet
Lösungen:
- EB-Wellen gegenüber B-Wellen bevorzugen
- Die Shore-Härte und Eigenschaften der Druckplatte überprüfen
- Die Druckplatte wechseln
- Die WPA-Einstellungen optimieren
Fragen und Antworten zu Druckfehlern auf Papier & Karton
Gründe:
- Diese Farbvariationen werden hauptsächlich bei Quetschrakelsystemen beobachtet, wenn Gummiwalze und Rasterwalze nicht parallel zueinander eingestellt sind
Lösungen:
- Gummiwalze und Rasterwalze parallel einstellen
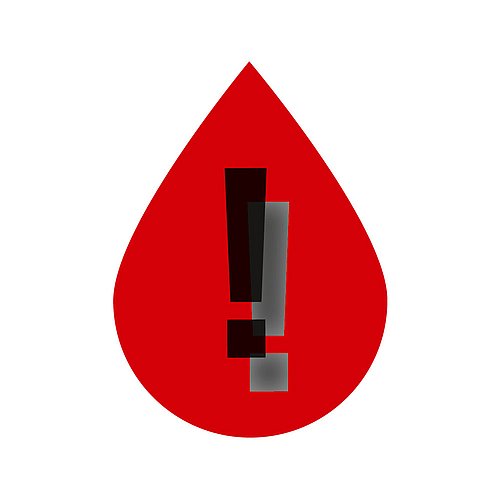
Gründe:
- Ungenügende Trocknung zwischen den zwei Farben
- Die Zellen der Rasterwalze sind nicht ausreichend gefüllt
- Die Druckgeschwindigkeit ist zu hoch
- Die Viskosität der Druckfarbe ist zu hoch
- Die Druckfarben werden in der falschen Reihenfolge gedruckt
Lösungen:
- Die Effizienz der Trocknung oder die Farbrezepturen überprüfen; gegebenenfalls Verzögerer hinzufügen
- Den Druck im Kammerrakelsystem erhöhen
- Die Druckgeschwindigkeit oder die Viskosität verringern
- Die Viskosität durch Zugabe von Wasser reduzieren
- Die Farbreihenfolge ändern
Gründe:
- Zu hoher Farbauftrag auf die Druckplatte
- Die Druckplatte ist abgenutzt, die Tiefe des Reliefs ist zu gering
- Der Anpressdruck zwischen dem Druckzylinder und dem Substrat ist zu hoch
- Die Druckgeschwindigkeit ist zu niedrig
- Die Viskosität ist zu hoch
Lösungen:
- Anpassung des Anpressdrucks der Rasterwalze und/oder des Kammerrakels
- Die Druckplatte waschen oder ersetzen
- Den Anpressdruck reduzieren
- Die Druckplatte reinigen und die Druckgeschwindigkeit erhöhen
- Die Viskosität durch Zugabe von Wasser reduzieren
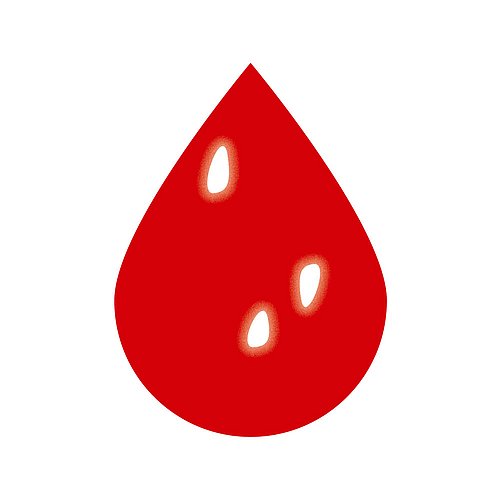
Gründe:
- Die Bogenzufuhr ist nicht sauber
- Die Druckplatte ist verschmutzt oder die Umgebung zu staubig
- Das Substrat ist staubig
Lösungen:
- Die Bogenzufuhr reinigen
- Die Druckplatte reinigen
- Das Substrat vor der Maschinenzufuhr mit einer effizienten Bahnreinigungsanlage reinigen Einsatz einer antistatischen Einheit oder antistatischer Bürsten in Betracht ziehen
Gründe:
- Durch unsachgemäßes Rühren wird der Druckfarbe zu viel Luft zugeführt
- Die Viskosität der Druckfarbe ist zu hoch
- Einsatz falscher Druckfarbe/Druckfarbe ist für den Auftrag nicht angemessen
Lösungen:
- Die Pumpgeschwindigkeit und die Farbschläuche auf Undichtigkeiten überprüfen
- Farbzufuhr und -rückfuhr optimieren
- Pumpgeschwindigkeit regulieren
- Rührer verwenden und auf optimalen Füllstand der Druckfarbe achten
- Die Viskosität durch Zugabe von Wasser reduzieren
- Ein alternatives Rezept formulieren
- Entschäumer hinzufügen und kontinuierlich rühren
Übermäßige und fehlerhafte Zugabe von Entschäumer führt zur Bildung von Fischaugen, in diesem Fall ist die Druckeinheit zu reinigen und mit frischer Druckfarbe zu befüllen.
Gründe:
- Helle Streifen: Ablagerungen auf dem Kammerrakel
- Dunkle Streifen: Verformung oder Abnutzung des Kammerrakels
- Die Rasterwalze ist beschädigt
- Die Rasterwalze ist durch angetrocknete Druckfarbe verschmutzt
- In der Druckfarbe sind Partikel vorhanden
Lösungen:
- Das Kammerrakel reinigen oder ersetzen
- Das Kammerrakel ersetzen
- Die Rasterwalze ersetzen
- Die Rasterwalze reinigen
- Druckfarbe ersetzen und Druckplatten, Kammerrakel, Rasterwalze sowie Pumpe inkl. Schläuchen reinigen
Gründe:
- Die Druckplatte ist schmutzig, beschädigt oder brüchig
- Die Druckfarbe trocknet zu schnell
- Die Druckeinstellung zwischen Druckzylinder und Substrat ist zu niedrig
- Die Druckplatte ist verschmutzt oder die Umgebung ist zu staubig
Lösungen:
- Die Druckplatte reinigen oder ersetzen
- Einen Verschnitt einsetzen, der langsamer trocknet
- Höhere Druckeinstellungen verwenden
- Die Druckplatte reinigen
Gründe:
- Unvollständige Benetzung des Substrats
- Zu viel Druckfarbe auf der Rasterwalze
Lösungen:
- Durch Zugabe eines Benetzungsmittels wird die Oberflächenspannung gesenkt und eine vollständige Benetzung des Substrats und somit ein besserer Verlauf der Farbe ermöglicht
- Das Farbvolumen reduzieren, indem eine Rasterwalze mit geringerem Schöpfvolumen eingesetzt wird
- Verringerung der Viskosität
Gründe: Die Druckplatte ist der Ursprung für das Problem: ·
- Rasterwinkel ist nicht korrekt
- Rasterlinien variieren für die einzelnen Druckfarben
- Das Verhältnis zwischen Linienanzahl der Rasterwalze und der Druckplatte ist zu niedrig
Lösungen:
- Eine neue Druckplatte erstellen
- Das Verhältnis sollte größer als 4 sein
- Für ein 48er Raster mindestens eine 200er Rasterwalze verwenden
Gründe:
- Ein gestrichenes Substrat wird verwendet
Lösungen:
- Keine gestrichenen Substrate ohne Trocknung verwenden
- Schnelltrocknende Farben einsetzen
- Den Druck lackieren
- Ein Wachsadditiv unter Rühren hinzufügen
Gründe:
- Die Rasterwalze ist verschmutzt. Bereiche, die mit Farbresten zugesetzt sind, verursachen helle Flecken.
- Auf Grund der Wiederholung vorhergehender Druckaufträge erzeugen saubere Bereiche dunkle Flecken
- Die Druckplatte ist beschädigt z. B. Kratzer, Falten, Risse
- Die Druckfarbe ist inhomogen z. B. durch Restwasser in der Druckeinheit
Lösungen:
- Die Rasterwalze reinigen
- Eine neue Druckplatte erstellen
- Falls in der Druckeinheit Wasser zurückgeblieben ist, wird dieser Effekt nach einigen Druckbögen nicht mehr auftreten
- Die Druckfarbe rühren, Viskosität überprüfen
Dieser Druckfehler kann auch im Rasterdruck auftreten
Gründe:
- Die Rasterwalze ist abgenutzt
- Die Viskosität der Druckfarbe ist zu niedrig
- Die Druckgeschwindigkeit ist zu gering
Lösungen:
- Die Rasterwalze erneuern
- Die Viskosität durch Zugabe frischer Druckfarbe erhöhen
- Eine Erhöhung der Druckgeschwindigkeit reduziert die Streifenbildung
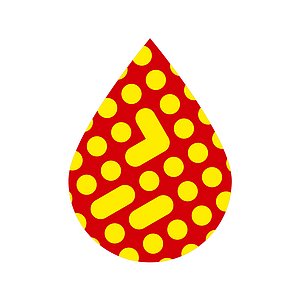
Gründe:
- Das übertragene Farbübertragungsvolumen ist zu hoch
- Die Rasterwalze und die Rasterweite der Druckplatte sind nicht optimal aufeinander abgestimmt
- Das Verhältnis zwischen Rasterweite des Klischees und Rasterweite der Rasterwalze ist zu gering
- Die Viskosität der Druckfarbe (Auslaufzeit DIN 4 mm Cup) ist zu hoch
Lösungen:
- Eine Rasterwalze mit niedrigerem Schöpfvolumen einsetzen
- Eine Rasterwalze mit höherer Liniatur einsetzen
- Eine angepasste Druckplatte anfertigen lassen
- Die Auslaufzeit mit Wasser einstellen