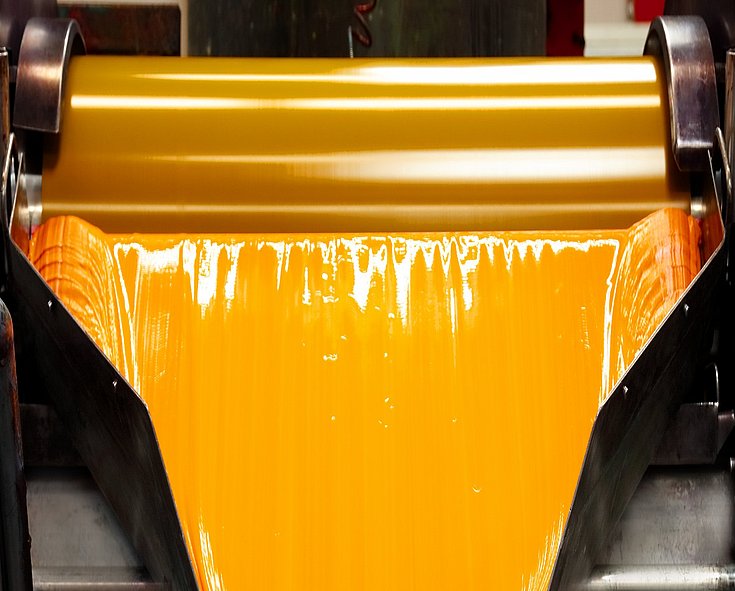
Colors are passion, emotions and personality. At Siegwerk, inks and coatings are our specialty and we use color to bring the packaging and products of our customers to life.
What role do barrier coatings play in mono-material packaging for food applications?
Most foods are sensitive to contact with one or more external factors such as oxygen or humidity. Successful food preservation therefore depends on the packaging's ability to protect the food from these external influences – as effectively as possible and for as long as possible. Thus, it's all about providing the barrier properties and resistance needed to protect the contents during transport, extend its shelf life and thus prevent food spoilage. The answer to all these requirements has long been the use of multi-material structures. However, these types of packaging are also some of the most difficult to recycle because they often can’t be separated into their individual components, which can significantly affect the recycling process and thus the quality of the recyclate. A more sustainable alternative to meet the demand of circularity is mono-material structures made from recyclable materials such as PE or PP. However, these have to be equipped with the necessary barrier properties to preserve and protect the packed food as intended. And this is where barrier coatings come into play. They provide mono-materials with the appropriate barriers and can be recycled with the packaging material without adversely affecting the recycling process or the recyclate.
Last year, Siegwerk and DG Press jointly developed a coffee pouch made of mono-PE material with an oxygen barrier coating. Can you tell us a bit more about this?
Sure. First of all, you need to know that coffee is extremely sensitive to oxygen, moisture and UV light. Proper packaging must therefore provide the appropriate barriers to preserve the quality, aroma and taste of the coffee. The final barrier requirements can vary depending on the type of coffee, whether it is whole bean or ground, single serve or instant. In our development project with our partner DG Press, we focused on mono-material packaging for ground coffee and coffee beans. For this, our oxygen barrier coating was applied to a laminated PE film structure (MDO-PE//PE), overprinted with inks and finished with a heat-resistant matt coating to enable sealing and protect the oxygen barrier from moisture. The result was a mono-material, quad-seal coffee pouch with a high oxygen barrier that has been shown to not only preserve taste and composition of the packed coffee, but also to be recyclable yielding a very high quality recyclate. This innovative mono-material pouch design was also recognized with the Sustainability Hero Award 2024 last year.
So, barrier coatings play a key role in realizing high-performance mono-material packaging, especially for food. Can you tell us a little more about the coatings used?
Both used coatings are part of Siegwerk’s CIRKIT range of functional coatings especially designed for packaging circularity. The CIRKIT OxyBar BC 1582 is an innovative oxygen barrier coating that ensures a prolonged shelf life especially for dry food packaging applications. The coating can be applied on both flexo and gravure presses at industrial machine speeds on various substrates, giving excellent transparency. Next to an enhanced oxygen barrier, this coating also enables superior deinkability during the recycling process under DIN conditions. With CIRKIT Heatguard, in turn, we offer a range of heat-resistant coatings that ensure a good performance on high-speed FFS (Form, Fill and Seal) lines with mono-PE structures. They have excellent rub and scratch resistance and thus enable surface print structures.
You recently conducted further tests on this mono-PE coffee packaging. What exactly was tested and why?
Correct. In collaboration with KLEVERTEC, a German research institute for food and packaging technology, we conducted an independent shelf life test on packed coffee beans and ground coffee. For this purpose, the beans were stored for 36 weeks at room temperature, i.e. at a constant temperature of 23°C and a constant relative humidity of 50%. They were packed in the pouch described above, consisting of a laminated PE film structure coated with our oxygen barrier coating (MDO-PE//PE). For comparison purposes, the coffee beans were also packed in a PE-pouch with EVOH in the film (MDO-PE//PE-EVOH-PE) that was also equipped with our oxygen barrier coating. After 12, 24 and 36 weeks of storage, sensory tests were conducted to determine whether the differently packed coffees differed significantly. The aim of the test was to rule out any significant loss of aroma due to the absence of an EVOH barrier. In other words, we wanted to see if a mono-PE packaging with only a barrier coating and no EVOH is as suitable for storing coffee as one with EVOH.
Why did you use an EVOH-based structure for comparison?
Well, EVOH films are used in many food packaging solutions because of their well-known superior barrier properties. In the case of coffee packaging, EVOH film offers a very good oxygen barrier that prevents oxidative degradation of the coffee flavor, reduces the release of coffee aroma and prevents the absorption of foreign aromas from the environment. For comparison purposes during the development project with DG Press, we had already produced an additional pouch version based on a PE film with EVOH. This version was now included in the shelf life test.
Can you tell us a bit more about the testing method? How is packaging tested for shelf life performance?
The sensory tests were conducted as triangle tests, which means that each participant was given three samples to test, two of which were identical and the third of which had to be identified. The samples were presented in such a way that no visual differences could be perceived. Three different aspects were tested: the smell of ground coffee, the smell of brewed coffee and the taste of brewed coffee. To ensure comparability, the coffee was ground to a specific consistency and the brewed coffee was prepared using a standard filter coffee method with clear parameters, including serving temperature. At the end, the calculated scores indicated whether or not there was a statistically significant difference between the samples.
And what were the test results? How did the mono-PE pouch with barrier coating perform?
Both the odor test in ground and brewed form and the taste test in brewed form showed no significant differences between the barrier properties of the two packaging structures tested. The panel participants could not detect any loss of aroma or the development of off-flavors. Therefore, it can be assumed that coffee packed in a mono-PE pouch only equipped with our oxygen barrier coating does not suffer any noticeable deterioration over a storage period of 36 weeks at room temperature. This result indicates that our barrier coating protects the coffee from harmful influences just as well as an EVOH film. In other words, there is no loss of aroma due to the absence of an EVOH barrier.
With these results, we would like to invite converters and brand owners to test our new coatings and jointly create effective and sustainable mono-material packaging structures with enhanced functionality and recyclability.
To learn more about Siegwerk’s coatings, please visit https://www.siegwerk.com/en/inks-coatings/coatings.html.