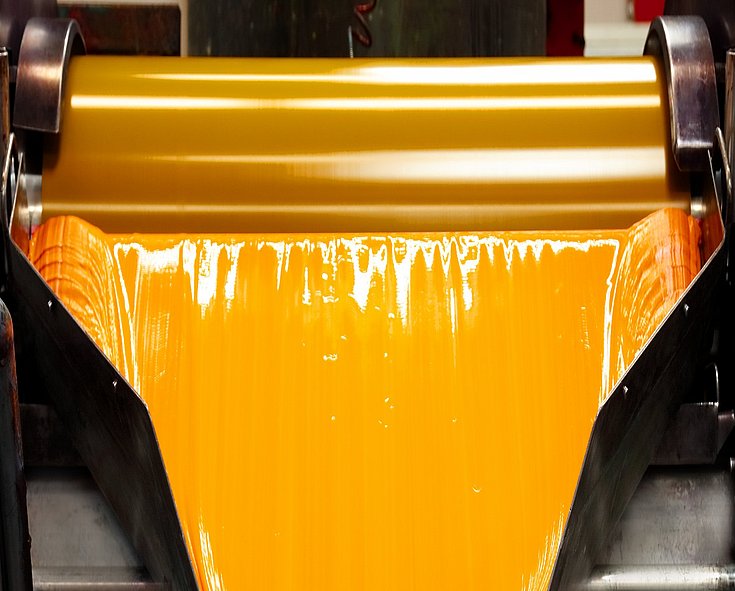
Colors are passion, emotions and personality. At Siegwerk, inks and coatings are our specialty and we use color to bring the packaging and products of our customers to life.
Printers are caught between constant cost pressures and increasing competition. Cost reductions as well as productivity and efficiency increases are the major variables that determine whether printers are successful or not.
Q: Next to inks, Siegwerk also offers its customers consultancy services. Of what kind of services are we talking?
A: No process is so good that you can’t improve it – often all that’s missing is an objective perspective from an industry expert. With our On-Site Consulting (OSC), we take an integrated look at processes to try and identify possible efficiency increases and savings potential, which enables us to generate real added value for the customer. As part of our InHouse service we also provide expert support in ink preparation directly at the customer’s site – our aim is to get the maximum out of any inkroom.
Q: How exactly does the On-Site Consulting service work?
A: Together with the customer, our OSC experts analyze production processes along the entire workflow chain – from pre-press via ink management and print room performance to finishing. This analysis is then used to identify potential savings, enhance procedures and resources and draft action plans for a sustainable implementation. Given their many years of experience in the print industry, our experts are optimally equipped to achieve production increases at no less than the same level of print quality and to optimize a customer’s total cost of ownership.
Q: How does that work out in practice?
A: In addition to setup times and downtimes, we also analyze the level of waste that is generated during the process, like for example wastage of setup materials. In setup workshops we can identify not ideally positioned tools and materials including path and time analyses. Furthermore, we support customers with optimum ink preparation and provide assistance with the conceptual design of new dispensing systems and more environmentally compatible production. Experiences show that six-figure Euro amounts can thus be saved.
Q: What other forms of support do you provide apart from consultancy services?
A: We see us as coach unleashing new ideas and thus helping the customer to achieve sustainable business development. We want to enable our customers to implement enhancements in a continuous and sustainable manner. For this purpose, we offer a wide range of training modules that cover topic areas like lean production and process optimization as well as colorimetry and inkroom organization. These modules can be conducted either at Siegwerk or at the customer’s site.