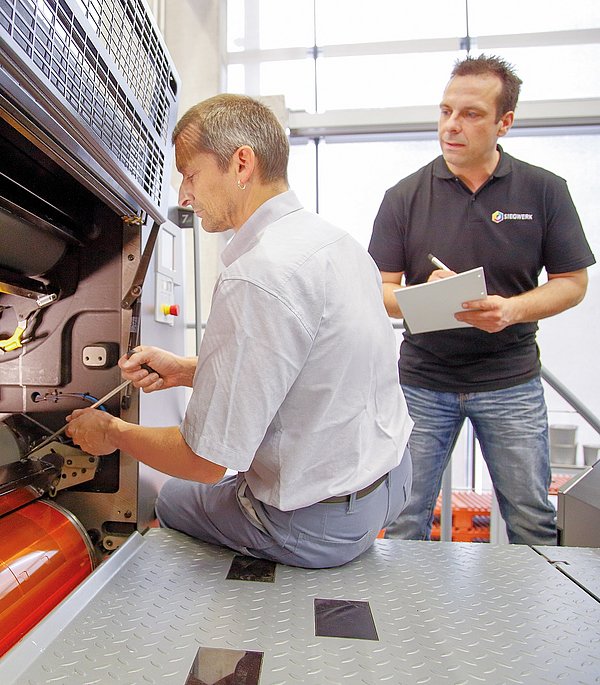
Flexodruck Ratgeber
Der Flexodruck Ratgeber von Siegwerk bietet Ihnen die Möglichkeit, Probleme schnell zu erkennen und zu beheben und so die Produktivität im Druck zu steigern.
Fragen und Antworten zum Thema Blockieren
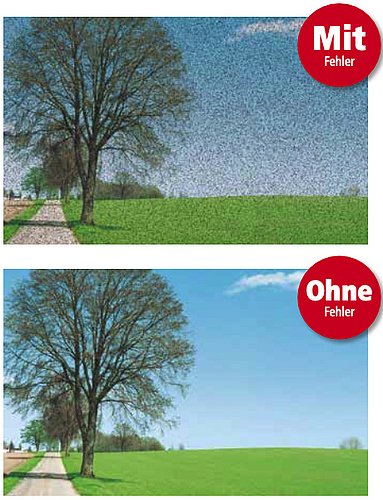
Die Farbe haftet auf der Rückseite der Folie an und verursacht dabei Beschädigungen, wenn der Bedruckstoff abgerollt wird.
Ursache 1
- Es ist zu viel Verzögerer in der Farbe.
Abhilfe
- Ersetzen Sie die Farbe.
Ursache 2
- Die Folientemperatur an der Aufwicklung ist zu hoch.
Abhilfe
- Verringern Sie die Temperatur des Tunneltrockners und überprüfen Sie, ob die Kühltrommel funktioniert.
Ursache 3
- Vorbehandlungsniveau der Folie ist zu niedrig.
Abhilfen
- Überprüfen Sie die Vorbehandlung und das Alter der Folie.
- Verwenden Sie die Inline-Coronabehandlung.
Ursache 4
- Die Farbtrocknung ist zu langsam.
Abhilfen
- Erhöhen Sie die Trocknerleistung.
- Verwenden Sie ein schneller trocknendes Lösungsmittel.
- Verringern Sie die Druckgeschwindigkeit.
Ursache 5
- Das übertragene Farbvolumen ist zu hoch.
Abhilfe
- Wählen Sie Rasterwalzen mit niedrigerem Schöpfvolumen.
Ursache 6
- Die Farbviskosität ist zu hoch.
Abhilfe
- Verringern Sie die Farbviskosität durch Hinzufügen von Lösungsmitteln.
Ursache 7
- Die Kühlung funktioniert nicht.
Abhilfe
- Setzen Sie sich mit dem Wartungsdienst in Verbindung.
Ursache 8
- Zu hoher Wickeldruck an der Aufwicklung
Abhilfe
- Verringern Sie die Wickelspannung.
Ursache 9
- Die aufgewickelte Bahn hat eine zu hohe Feuchtigkeit.
Abhilfen
- Erhöhen Sie die Trocknerleistung zwischen den Druckwerken und reduzieren Sie die Kühlung.
Ursache 10
- Beschichtung oder Vorbehandlung auf beiden Seiten der Folie.
Abhilfe
- Überprüfen Sie, ob das richtige Farbsystem verwendet wird.
Fragen und Antworten zum Flypaper-Effekt
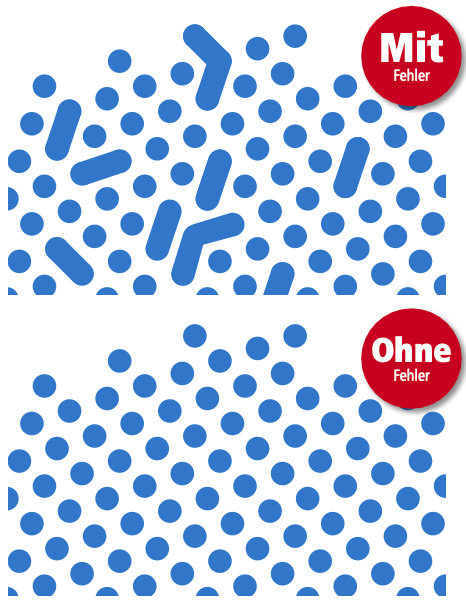
Es werden Farbverbindungen zwischen einzelnen Rasterpunkten der Druckplatte erzeugt. Die Zwischentiefen werden mit Farbe gefüllt.
Ursache 1
- Die relative Luftfeuchtigkeit ist zu hoch.
- Wasser kondensiert in die Lösungsmittelfarben.
Abhilfen
- Ersatz durch frische Farbe.
- Passen Sie die Lösungsmittelmischung an.
- Erhöhen Sie Trocknerleistung zwischen den Druckwerken.
Ursache 2
- Die Farbrezeptur passt nicht zum Druckmotiv.
Abhilfe
- Ersetzen Sie die Farbe.
Ursache 3
- Falsche Wahl des Lösungsmittels.
- Die Farbe trocknet zu schnell.
Abhilfen
- Leeren Sie den Farbtank und passen Sie die Lösungsmittelmischung an.
Ursache 4
- Die Farbviskosität ist zu hoch.
Abhilfe
- Verringern Sie die Viskosität.
Ursache 5
- Das Schöpfvolumen ist zu hoch.
Abhilfe
- Wählen Sie für den Druckauftrag Rasterwalzen mit geringerem Schöpfvolumen.
Ursache 6
- Die Rasterwalze und Klischeerasterweite passen nicht zusammen.
Tonwertzunahme beim Flexodruck: Fragen und Antworten
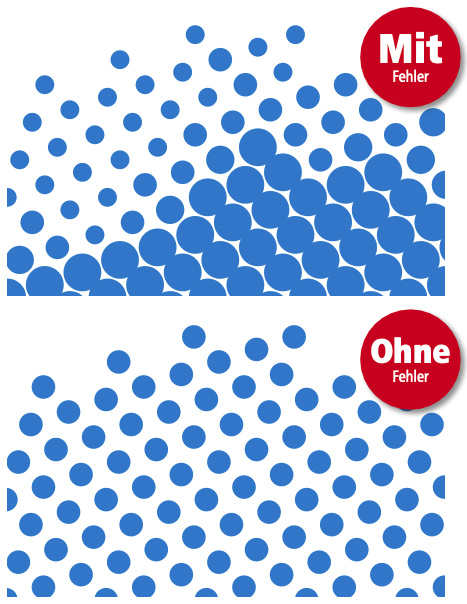
Zu hohe Tonwertzunahme auf dem Bedruckstoff. Sie verringert die Zeichnung und den Kontrast.
Ursache 1
- Die Dickentoleranz der Druckplatte oder des doppelseitigen Klebebandes ist zu groß.
Abhilfe
- Wechseln Sie die Druckplatte oder das doppelseitige Klebeband.
Ursache 2
- Die Druckplatte ist zu weich oder das doppelseitige Klebeband zu hart.
Abhilfe
- Ersetzen Sie die Druckplatte oder das Klebeband.
Ursache 3
- Die Druckbeistellung zwischen Plattenzylinder und Bedruckstoff ist zu hoch.
Abhilfe
- Verringern Sie die Druckbeistellung.
Ursache 4
- Die Dickentoleranz der Folie ist zu hoch.
Abhilfe
- Verringern Sie den Druck des Plattenzylinders oder ersetzen Sie die Bedruckstoffrolle.
Ursache 5
- Die Tonwertzunahme wurde falsch berechnet.
Abhilfe
- Passen Sie die Kurve der Tonwertzunahme entsprechend an.
Ursache 6
- Die Temperatur des Zentralzylinders ist zu hoch oder zu niedrig.
Abhilfe
- Setzen Sie sich mit dem Wartungsdienst in Verbindung.
Fragen und Antworten zur Farbstärke
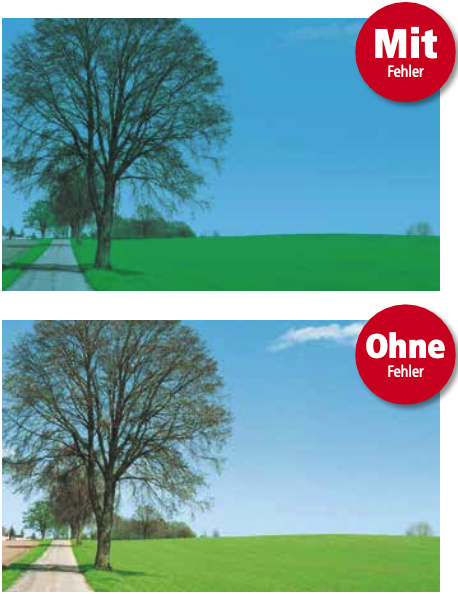
Die Farbstärke ist im Vergleich zu vorherigen Drucken oder Mustern zu hoch.
Ursache 1
- Das Schöpfvolumen der Rasterwalze ist zu hoch.
Abhilfe
- Verwenden Sie eine Rasterwalze mit geringerem Schöpfvolumen.
Ursache 2
- Die Farbviskosität ist zu hoch.
Abhilfe
- Fügen Sie Lösungsmittel und/oder Verschnitt hinzu, um die Farbviskosität anzupassen.
Ursache 3
- Die Farbrezeptur bei der Farbabstimmung ist zu kräftig.
Abhilfen
- Fügen Sie Verschnitt hinzu.
- Optimieren Sie die Farbrezeptur.
Ursache 4
- Die Einstellungen des Rakels sind falsch.
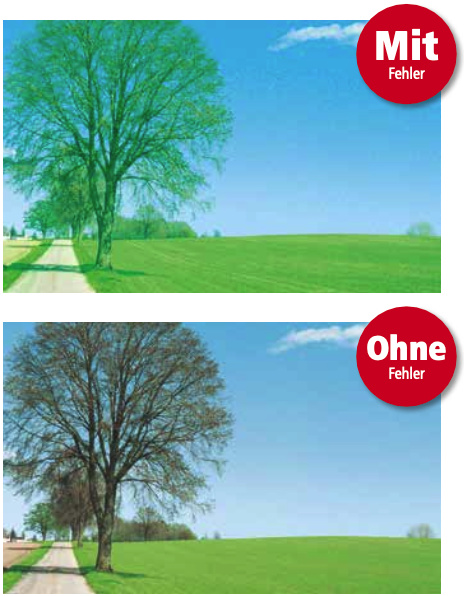
Farbstärke ist im Vergleich zu vorherigen Drucken oder Mustern schwächer.
Ursache 1
- Die Farbe trocknet an den Rasterwalzen an.
Abhilfen
- Reinigen Sie die Rasterwalze.
- Zu hohe oder zu niedrige Druckbeistellung zwischen Plattenzylinder und Bedruckstoff oder zwischen Rasterwalze und Druckplatte.
Ursache 2
- Die verwendete Druckfarbe ist zu farbschwach.
Abhilfen
- Wenden Sie sich an Ihren Farblieferanten oder
- fügen Sie – sofern möglich – eine konzentrierte Farbe hinzu.
Ursache 3
- Die Farbe ist zu dünn.
Abhilfe
- Erhöhen Sie die Viskosität durch frische Farbe.
Ursache 4
- Die Rasterwalze ist verschlissen.
Abhilfe
- Wechseln Sie die Rasterwalze.
Ursache 5
- Die Farbe ist defekt.
Abhilfe
- Ersetzen Sie diese durch frische Farbe.
Ursache 6
- Zu hohe oder geringe Druckbeistellung zwischen dem Plattenzylinder und dem Bedruckstoff oder zwischen der Rasterwalze und dem Plattenzylinder.
Abhilfe
- Passen Sie die Druckbeistellung an.
Ursache 7
- Die Farbe ist aufgrund zu hoher Maschinenstillstandzeit angetrocknet.
Abhilfen
- Reinigen Sie die Druckplatte und die Rasterwalze.
Ursache 8
- Es wurde eine Rasterwalze mit zu geringem Schöpfvolumen verwendet.
Abhilfe
- Wählen Sie eine Rasterwalze mit höherem Schöpfvolumen.
Fragen und Antworten zu Rasterpunkten
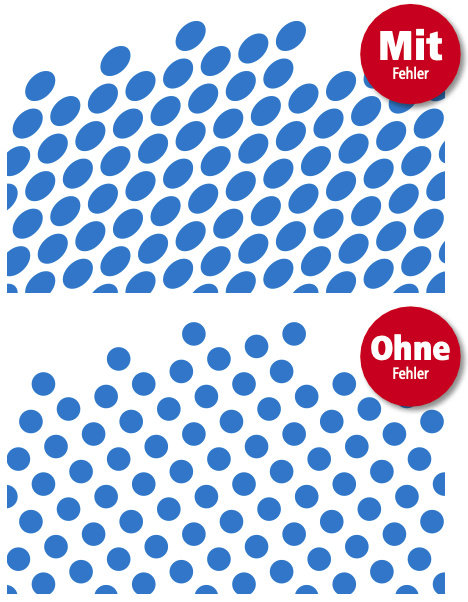
Die Rasterpunktform im Druck weicht von der Originalpunktform deutlich ab.
Ursache 1
- Die Druckbeistellung zwischen dem Plattenzylinder und dem Bedruckstoff ist zu hoch.
Abhilfe
- Verringern Sie die Druckbeistellung.
Ursache 2
- Die Bahnspannung ist zu niedrig.
Abhilfe
- Regulieren Sie die Bahnspannung.
Ursache 3
- Zu große Dickenschwankungen der Druckplatte oder des doppelseitigen Klebebandes.
Abhilfen
- Wechseln Sie die Druckplatte oder vewenden Sie ein anderes Klebeband.
Ursache 4
- Die Relieftiefe der Druckplatte ist zu hoch.
Abhilfe
- Benutzen Sie eine Druckplatte mit geringerer Relieftiefe.
Ursache 5
- Es gibt eine Geschwindigkeitsdifferenz zwischen Platten- und Gegendruckzylinder.
Abhilfe
- Überprüfen Sie die Stärke des doppelseitigen Klebebandes und der Druckplatte.
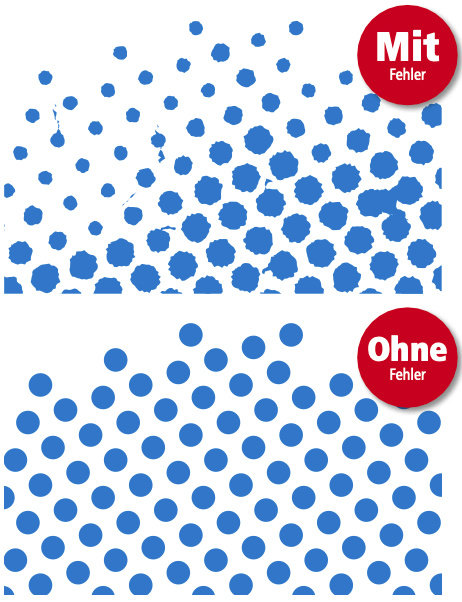
Ungleichmäßige Kanten um den Rasterpunkt.
Ursache 1
- Die Farbe trocknet auf Druckplatte ein.
Abhilfe
- Reinigen Sie die Druckplatte und passen Sie die Lösungsmittelmischung an.
- Fügen Sie Verzögerer hinzu.
- Vergewissern Sie sich, dass das Heißluftgebläse nicht auf die Druckerplatte bläst.
Ursache 2
- Die Druckbeistellung zwischen der Rasterwalze und dem Plattenzylinder ist zu hoch.
Abhilfe
- Reduzieren Sie die Druckbeistellung.
Ursache 3
- Die Farbviskosität ist zu hoch.
Abhilfe
- Passen Sie die Farbviskosität durch Hinzufügen von Lösungsmitteln an.
Ursache 4
- Die Flusen vom Reinigungstuch sind auf der Druckplatte.
Abhilfe
- Reinigen Sie die Druckplatte.
- Verwenden Sie ein flusenfreies Reinigungstuch oder eine Reinigungsbürste.
Ursache 5
- Die Farbrezeptur passt nicht zum Druckmotiv.
Abhilfe
- Ersetzen Sie die Farbe.
Ursache 5
- Die Druckbeistellung zwischen dem Plattenzylinder und dem Bedruckstoff ist zu hoch.
Abhilfe
- Reduzieren Sie die Druckbeistellung.
Fragen und Antworten zum Ghosting Effect (Geisterbilder-Effekt)
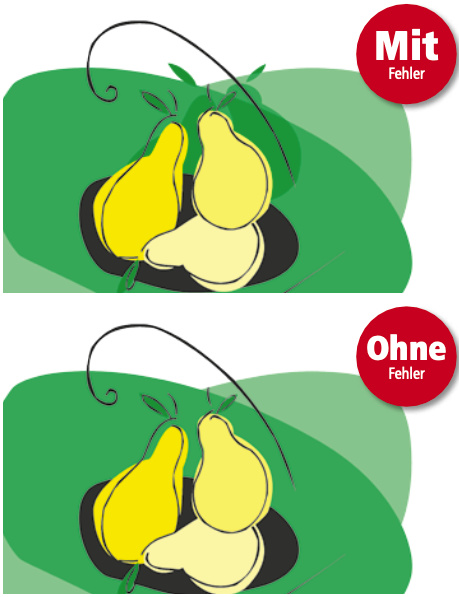
Der Geistereffekt ist ein schwaches Druckbild, das an einer Stelle des Motivs sichtbar wird, wo es nicht sein sollte. Üblicherweise tritt dieser Effekt beim Volltondruck mit negativen Schriften oder mit Fenstern auf.
Ursache 1
- Das Farbangebot ist zu gering, da das Schöpfvolumen der Rasterwalze zu niedrig ist.
Abhilfe
- Verwenden Sie eine Rasterwalze mit höherem Schöpfvolumen.
Ursache 2
- Die Farbe trocknet in den Näpfchen.
Abhilfe
- Fügen Sie der Farbe Verzögerer hinzu.
Ursache 3
- Die Näpfchen sind unzureichend befüllt.
Abhilfe
- Erhöhen Sie den Druck im Kammerrakelsystem.
Ursache 4
- Die Druckgeschwindigkeit ist zu gering.
Abhilfe
- Erhöhen Sie die Druckgeschwindigkeit oder die Viskosität der Farbe.
Fragen und Antworten zum Thema Halo-Effekt
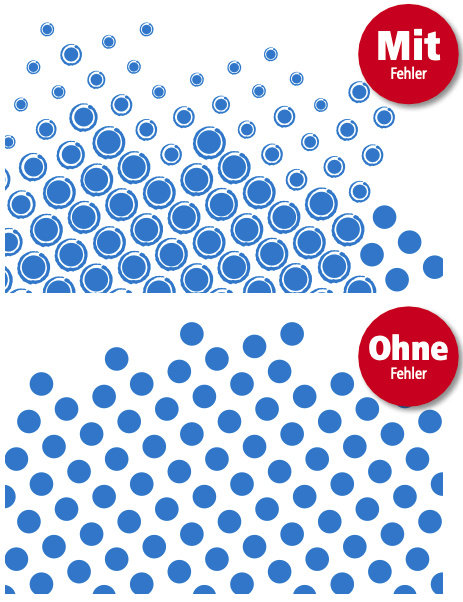
Der Rasterpunkt wird von einer Linie bzw. einem Ring umschlossen.
Ursache 1
- Es gibt eine Geschwindigkeitsdifferenz zwischen Platten- und Gegendruckzylinder.
Abhilfe
- Überprüfen Sie die Stärke des doppelseitigen Klebebandes und der Druckplatte.
Ursache 2
- Das Schöpfvolumen der Rasterwalze ist zu hoch.
Abhilfe
- Wählen Sie eine Rasterwalze mit geringerem Schöpfvolumen.
Ursache 3
- Die Druckbeistellung zwischen Plattenzylinder und Bedruckstoff ist zu hoch.
Abhilfe
- Verringern Sie die Druckbeistellung.
Ursache 4
- Der Druck des Kammerrakelsystems ist zu niedrig.
Abhilfe
- Erhöhen Sie den Druck im Kammerrakelsystem.
Ursache 5
- Die Druckbeistellung zwischen der Rasterwalze und dem Plattenzylinder ist zu hoch.
Abhilfe
- Reduzieren Sie die Druckbeistellung.
Fragen und Antworten zum Farbaufbau an Motivkanten
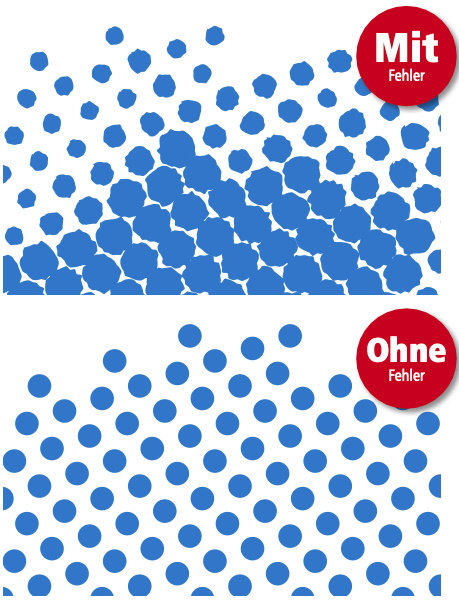
Farbaufbau an der Reliefkante des Rasterpunkts.
Ursache 1
- Das Schöpfvolumen der Rasterwalze ist zu hoch.
Abhilfe
- Das Schöpfvolumen der Rasterwalze ist zu hoch.
Ursache 2
- Die Druckgeschwindigkeit ist zu niedrig.
Abhilfen
- Die Druckgeschwindigkeit ist zu niedrig.
Ursache 3
- Die Farbviskosität ist zu hoch.
Abhilfe
- Reduzieren Sie die Viskosität.
Ursache 4
- Es wurden die falschen Lösemittel verwendet.
Abhilfe
- Ersetzen Sie die Farbe.
Ursache 5
- Die Druckbeistellung zwischen Plattenzylinder und Bedruckstoff ist zu hoch.
Abhilfe
- Verringern Sie die Druckbeistellung.
Ursache 6
- Die Farbrezeptur ist ungeeignet.
Abhilfe
- Ersetzen Sie die Farbe.
Ursache 7
- Die Druckplatte ist abgenutzt, die Relieftiefe ist zu gering.
Abhilfe
- Ersetzen Sie die Druckplatte.
Ursache 8
- Die relative Luftfeuchtigkeit ist zu hoch.
- Das Wasser kondensiert in die Lösemittelfarbe.
Abhilfen
- Passen Sie die Lösungsmittelmischung an – verwenden Sie Verzögerer und wasserfreies Lösungsmittel.
Fragen und Antworten zum Flächendruck
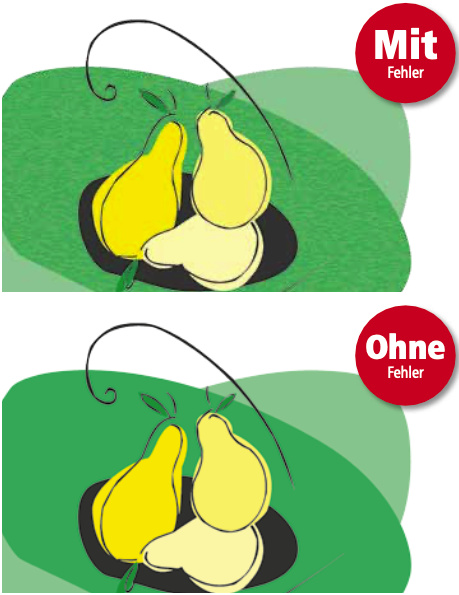
Gepunktetes oder unruhiges Druckbild der Vollfläche Schwache Farbstärke, körniger Flächendruck.
Ursache 1
- Die Oberfläche der Druckplatte ist wolkig/uneben.
- Eine Beschädigung der Oberfläche der Druckplatte ist erkennbar.
Abhilfe
- Neue Druckplatte herstellen.
Ursache 2
- Die Viskosität der Farbe ist zu niedrig.
Abhilfe
- Fügen Sie frische Farbe und/oder Verschnitt hinzu und sorgen Sie so für eine angemessene Viskosität.
Ursache 3
- Fremdkörper oder Verunreinigungen befinden sich auf dem Plattenzylinder oder der Rasterwalze.
Abhilfe
- Reinigen Sie den Plattenzylinder sorgfältig.
Ursache 4
- Die Oberfläche des Bedruckstoffes ist uneben.
Abhilfe
- Verwenden Sie weichere Druckplatten.
Ursache 5
- Die Farbe ist verunreinigt.
Abhilfe
- Filtrieren Sie die Farbe oder verwenden Sie frische Farbe.
Ursache 6
- Die Farbviskostiät ist zu hoch.
Abhilfe
- Fügen Sie der Farbe Lösungsmittel hinzu.
Ursache 7
- Der Rakeldruck ist zu hoch oder zu niedrig.
Abhilfe
- Passen Sie den Rakeldruck entsprechend an.
Druckfehlstellen beim Flexodruck
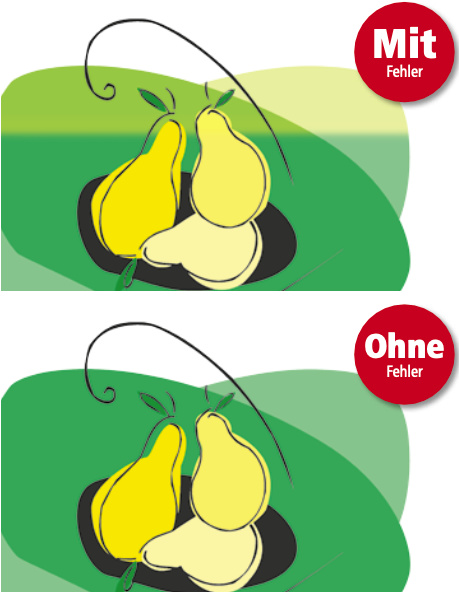
Fehlender Kontakt zwischen Bedruckstoff und Druckplatte oder zwischen Druckplatte und Rasterwalze führt zu mangelhafter Farbübertragung.
Ursache 1
- Die Dickenschwankungen der Druckplatte oder des doppelseitigen Klebebandes sind zu groß.
Abhilfe
- Wechseln Sie die Druckplatte oder
- das doppelseitige Klebeband aus.
Ursache 2
- Die Druckbeistellung ist zu niedrig.
Abhilfe
- Erhöhen Sie den Beistelldruck zwischen Plattenzylinder und Rasterwalze
- oder zwischen Plattenzylinder und Bedruckstoff.
Ursache 3
- Die Stärke des Bedruckstoffes ist außerhalb der Toleranz.
Abhilfe
- Erhöhen Sie den Beistelldruck des Plattenzylinders oder ersetzen Sie die Bedruckstoffrolle.
Ursache 4
- Der Plattenzylinder oder die Rasterwalze haben eine Unwucht.
Abhilfe
- Überprüfen Sie den Gang des Druckplattenzylinders (Konzentrizität usw.).
Ursache 5
- Das Schöpfvolumen der Rasterwalze ist zu niedrig.
Abhilfe
- Erhöhen Sie das Rasterwalzenvolumen.
Ursache 6
- Der Füllstand des Kammerrakels ist zu niedrig.
Abhilfen
- Erhöhen Sie das Farbniveau im Kammerrakel.
- Überprüfen Sie, ob die Farbpumpe richtig funktioniert.
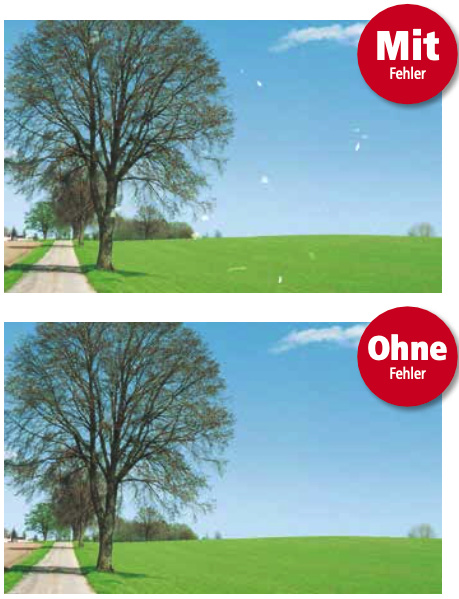
Staubpartikel auf dem Bedruckstoff verursachen Punkte und Mängelstellen. Dies ist beim Volltondruck der Fall, wobei dunkle Punkte von einem weißen ‚Heiligenschein’ umgeben werden.
Ursache 1
- Der Einzug ist verunreinigt.
Abhilfe
- Reinigen Sie den Einzug.
Ursache 2
- Die Druckplatte ist verunreinigt oder die Umgebung ist zu staubig.
Abhilfe
- Reinigen Sie die Druckplatte.
Ursache 3
- Fremdkörper befinden sich in der Rakelkammer.
Abhilfe
- Reinigen Sie das Farbzuführsystem.
Ursache 4
- Der Bedruckstoff ist statisch aufgeladen.
Abhilfe
- Verwenden Sie – sofern möglich – Antistatikrollen oder ersetzen Sie die Rolle.
Ursache 5
- Der Bedruckstoff ist verunreinigt.
Abhilfe
- Wechseln Sie den Bedruckstoff.
Ursache 6
- Die Einzugswalzen sind verunreinigt.
Abhilfe
- Reinigen Sie die Einzugswalzen.
Fragen und Antworten zum Thema Längsstreifen
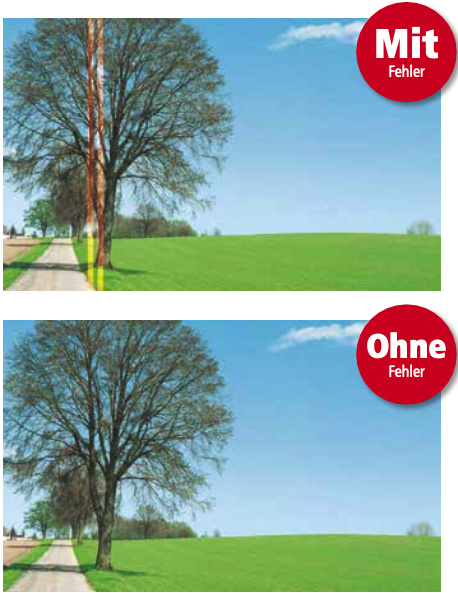
Fehldruck aufgrund von parallelen Linien in Druckrichtung.
Ursache 1
- Die Rakel ist verschlissen.
Abhilfe
- Ersetzen Sie die Rakel.
Ursache 2
- Auf der Rakel ist angetrocknete Farbe.
Abhilfe
- Reinigen Sie die Rakel.
Ursache 3
- Die Rasterwalze ist beschädigt.
Abhilfe
- Ersetzen Sie die Rasterwalze.
Ursache 4
- Die Rasterwalze ist blockiert oder der Antrieb der Rasterwalze ist fehlerhaft.
Abhilfe
- Setzen Sie sich mit dem Wartungsdienst in Verbindung.
Ursache 5
- Die Rasterwalze ist verunreinigt oder die Farbe auf der Rasterwalze ist angetrocknet.
Abhilfe
- Reinigen Sie die Rasterwalze.
Ursache 6
- Es befinden sich Partikel in der Farbe.
Abhilfe
- Reinigen Sie das Pumpensystem, die Druckplatten, die Rakel und die Rasterwalze, nachdem Sie die Partikel aus der Farbe gefiltert haben.
Fragen und Antworten zu mechanischen Beschädigungen
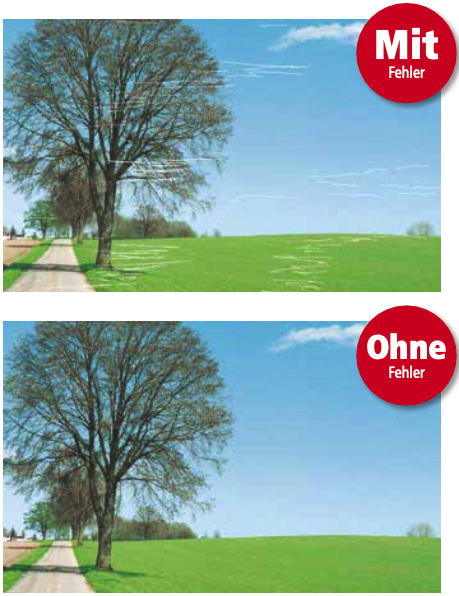
Unzureichende mechanische Beständigkeit des Druckes. Weitere Informationen finden Sie in unserer Broschüre‚ Schnelltests und Prüfverfahren zur Produktionskontrolle im Verpackungsdruck’.
Ursache 1
- Die Farbrezeptur ist ungeeignet oder die Farbe ist beschädigt.
Abhilfe
- Leeren Sie den Farbtank, reinigen Sie das Farbzuführsystem und ersetzen Sie die Farbe.
Ursache 2
- Das Schöpfvolumen der Rasterwalze ist zu hoch oder zu niedrig.
Abhilfe
- Wechseln Sie die Rasterwalze.
Ursache 3
- Es wurde ein ungeeignetes Lösemittel ausgewählt.
Abhilfe
- Verwenden Sie frische Farbe mit dem passenden Lösemittelgemisch.
Ursache 4
- Die Coronavorbehandlung der Folie ist zu gering.
Abhilfe
- Verwenden Sie eine Inline-Coronavorbehandlung.
Ursache 5
- Die Abriebfestigkeit ist mangelhaft.
Abhilfe
- Fügen Sie der Farbe ein Wachsadditiv hinzu.
Moiré-Effekt beim Flexodruck: FAQ
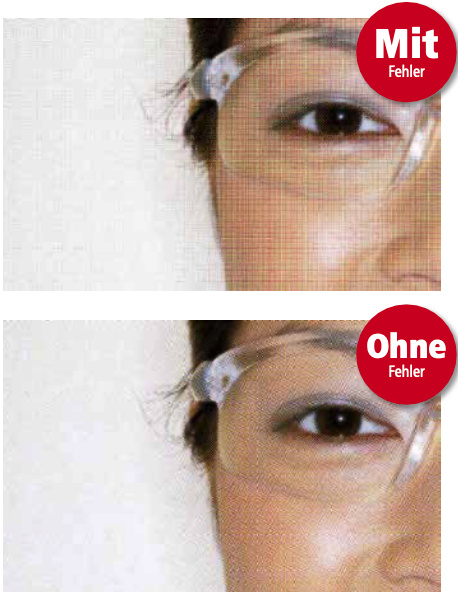
Im Übereinanderdruck der Skalenfarben (CYMK) können die einzelnen Rasterstrukturen interagieren und ein Muster erzeugen. Die Art der Interaktion kann ein unerwünschtes Interferenzmuster hervorrufen, der sogenannte Moiré-Effekt.
Ursache 1
- Die Rasterwinkelung auf der Druckplatte ist falsch.
Abhilfe
- Passen Sie die Rasterwinkelung in der Vorstufe an.
Ursache 2
- Das Verhältnis zwischen Linienzahl der Rasterwalze und der Rasterfeinheit der Druckplatte ist zu niedrig.
Abhilfe
- Das Verhältnis sollte größer 4 sein, verwenden Sie zum Beispiel für ein 48er Klischeeraster mindestens eine 200er Rasterwalze.
Ursache 3
- Die Farbe trocknet an Rasterwalze an.
Abhilfen
- Reinigen Sie die Rasterwalze.
- Fügen Sie der Farbe Verzögerer hinzu.
Ursache 4
- Eine falsche Abstimmung der Rasterwalzenwinkelung und der Rasterwinkelung auf den Druckplatten ist gegeben.
Abhilfe
- Wechseln Sie die Rasterwalze oder überarbeiten Sie die Repro mit geeigneteren Rasterwinkelungen.
Fragen und Antworten zum Thema Pinholes
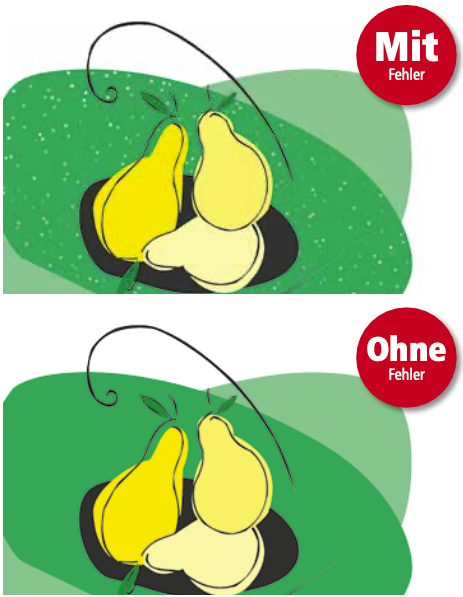
Pinholes sind kleine helle Stellen in der Volltondruckfläche.
Ursache 1
- Die Oberfläche der Folie oder der Druckplatte ist uneben.
Abhilfe
- Erhöhen Sie die Druckbeistellung oder ersetzen Sie die Folie oder die Druckplatte.
Ursache 2
- Der Bedruckstoff wird ungleichmäßig benetzt.
Abhilfe
- Verwenden Sie geeigneteren Bedruckstoff
- Erhöhen Sie die Farbschichtdicke durch höhere Viskosität oder Rasterwalzenwechsel.
Ursache 3
- Die Farbe schäumt.
Abhilfe
- Fügen Sie Entschäumer hinzu.
Ursache 4
- Der pH-Wert der Wasserfarben ist zu niedrig.
Abhilfe
- Führen Sie eine pH-Wert-Korrektur durch.
Ursache 5
- Die Druckbeistellung ist zu gering.
Abhilfe
- Erhöhen Sie die Druckbeistellung.
Ursache 6
- Es wurde eine falsche Weißfarbe gewählt.
Abhilfe
- Benutzen Sie eine geeignete Weißfarbe.
Passerprobleme beim Flexodruck
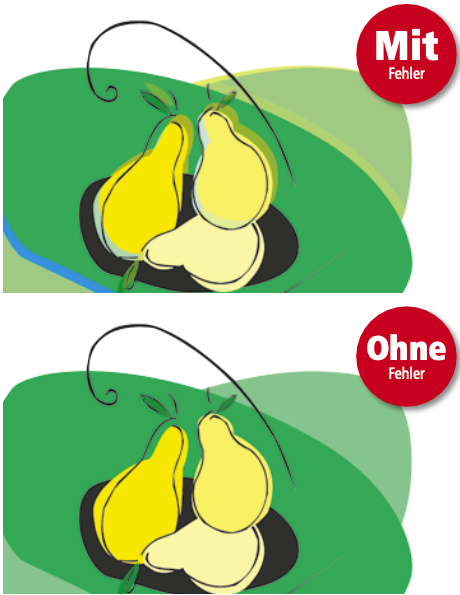
Im Zusammendruck passen die einzelnen Farben nicht deckungsgleich übereinander.
Ursache 1
- Die Druckplatte wurde falsch montiert.
Abhilfe
- Wiederholen Sie die Montage der Druckplatte.
Ursache 2
- Die Trocknertemperatur ist zu hoch.
Abhilfe
- Reduzieren Sie die Temperatur der Zwischenfarbtrockner.
Ursache 3
- Die Zugspannung der Bedruckstoffbahn ist falsch eingestellt.
Abhilfe
- Überprüfen Sie die Bahnspannung und kontrollieren Sie den Einzug und die Aufwicklung.
Ursache 4
- Die Dickenschwankungen des Bedruckstoffs sind zu hoch.
Abhilfe
- Ersetzen Sie die Bedruckstoffrolle.
FAQ zu veränderten Druckmotivlängen
Fragen und Antworten zum Thema Veränderung der Länge des Druckmotivs
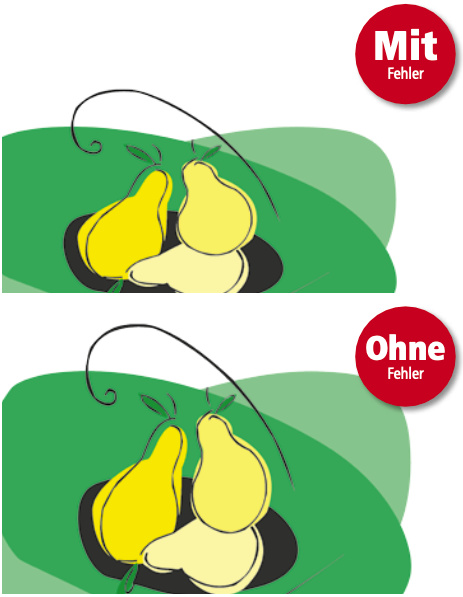
Das Druckmotiv in Druckrichtung ist zu kurz oder zu lang.
Ursache 1
- Die Bahnspannung ist zu hoch oder zu gering.
Abhilfe
- Passen Sie die Bahnspannung in Bezug auf die Eigenschaften des Bedruckstoffes an.
Ursache 2
- Die Dickenabweichung des Bedruckstoffs ist zu groß.
Abhilfe
- Wechseln Sie den Bedruckstoff.
Ursache 3
- Die Temperatur im Tunneltrockner ist zu hoch.
Abhilfe
- Verringern Sie die Temperatur im Tunneltrockner.
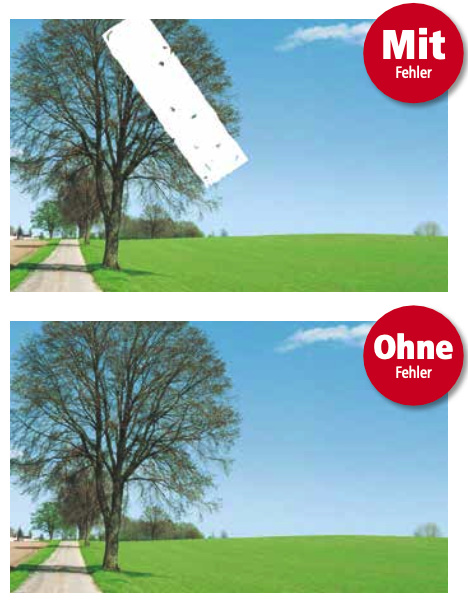
Ursache 1
- Ungeeignete Farbrezeptur oder falsches Farbsystem wurde verwendet.
Abhilfe
- Vergewissern Sie sich, dass das richtige Farbsystem verwendet wird.
Ursache 2
- Das Coronavorbehandlungsniveau der Folie ist zu niedrig.
Abhilfe
- Überprüfen Sie die Vorbehandlung und das Alter der Folie.
Ursache 3
- Die Wasserfarben haben einen deutlich zu niedrigen ph-Wert bei längeren Druckzeiten.
Abhilfe
- Benutzen Sie frische Farbe.
- Vergewissern Sie sich, dass die richtigen Lösungsmittel verwendet werden.
Ursache 4
- Die Haftung zwischen Farben ist zu schlecht.
Abhilfe
- Kann auftreten, wenn zwei unterschiedliche Farbsysteme übereinander gedruckt werden. Stellen Sie einen geeigneten Farbaufbau sicher.
Ursache 5
- Die Folienoberfläche ist verunreinigt.
Abhilfe
- Tragen Sie einen geeigneten Primer auf, bevor Sie mit dem Drucken beginnen, oder
- wechseln Sie auf eine geeignetere Folien-Charge.
Ursache 6
- Die Farbviskosität ist zu niedrig.
Abhilfe
- Erhöhen Sie die Viskosität mit frischer Farbe.
Ursache 7
- Mehrfarbiger Aufbau
Abhilfe
- Vergewissern Sie sich, dass die zuerst aufgetragene Farbe gute Anfangshaftung hat und nicht von der folgenden Farbe angelöst wird.
Ursache 8
- Die falsche Seite der Folie wurde bedruckt.
Abhilfe
- Überprüfen Sie die Folienseite.
Vergewissern Sie sich, dass das richtige Farbsystem verwendet wird.
Fragen und Antworten zu Querstreifen beim Flexodruck
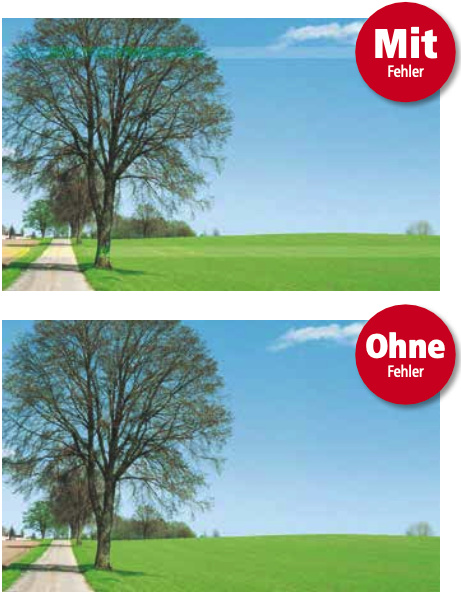
Fehldruck aufgrund von Linien quer zur Druckrichtung.
Ursache 1
- Der Durchmesser des Druckplattenzylinders und des verwendeten Zahnrades passen nicht zueinander.
Abhilfe
- Überprüfen Sie die die Abwicklungsmenge.
Ursache 2
- Die Druckbeistellung zwischen dem Plattenzylinder und dem Bedruckstoff ist zu hoch.
Abhilfe
- Verringern Sie die Druckbeistellung.
Ursache 3
- Die Druckgeschwindigkeit ist zu hoch.
Abhilfe
- Verringern Sie die Druckgeschwindigkeit.
Ursache 4
- Die Druckbeistellung zwischen der Rasterwalze und der Druckplatte ist falsch.
Abhilfe
- Passen Sie die Druckbeistellung an.
Ursache 5
- Es besteht ein mechanischer Fehler.
- Überprüfen Sie die mechanischen Teile der Druckmaschine.
Ausbluten und Abschmieren beim Flexodruck: FAQ
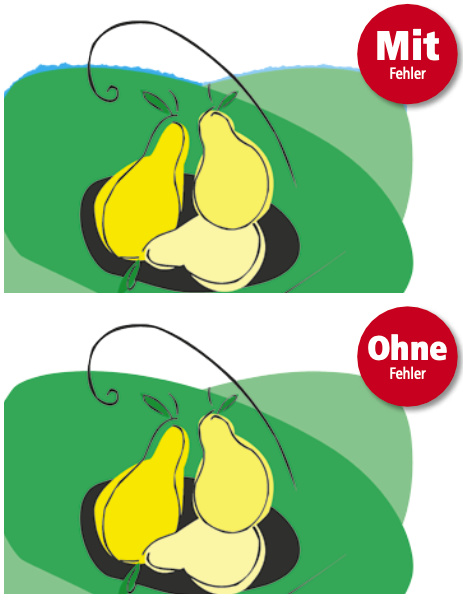
Von Ausbluten oder Abschmieren spricht man, wenn gefärbte Bestandteile der Druckfarbe in Motivteilen sichtbar werden, die nicht bedruckt wurden. Die vorherige Farbe muss trocken genug sein, um die nachfolgend aufzutragende Farbe aufnehmen zu können.
Ursache 1
- Die relative Luftfeuchtigkeit ist zu hoch.
- Kondensation von Wasser in die Lösemittelfarbe.
Abhilfen
- Verwenden Sie frische Farbe.
- Passen Sie die Lösemittelmischung an.
- Erhöhen Sie die Trocknerleistung und überprüfen Sie den Wassergehalt des Lösungsmittels.
Ursache 2
- Zu viel Verzögerer wurde verwendet.
Abhilfen
- Ersetzen Sie die Farbe durch frische Farbe.
- Verwenden Sie zur Verringerung ein schnelleres Lösungsmittel (beschleunigtes Trocknen).
Ursache 3
- Die Farbviskosität ist zu hoch.
Abhilfe
- Fügen Sie Lösungsmittel hinzu, um die Viskosität zu reduzieren.
Ursache 4
- Das Schöpfvolumen ist zu hoch.
Abhilfe
- Ersetzen Sie die Rasterwalzen.
Ursache 5
- Die Druckgeschwindigkeit ist zu hoch.
Abhilfen
- Verringern Sie die Druckgeschwindigkeit.
- Erhöhen Sie die Trockengeschwindigkeit der Farbe.
Ursache 6
- Nicht geeignete Farbmittel wurden in der Druckfarbe verwendet.
Abhilfe
- Stellen Sie eine neue Rezeptur zusammen, um die unerwünschten Farbmittel zu ersetzen.
Ursache 7
- Zu viele Farbschichten liegen übereinander.
Abhilfen
- Verringern Sie die Schichten.
- Entwerfen Sie ein neues Druckmotiv.